8 Reasons To Choose Permanent Mold Casting
Trying to decide if permanent mold is the right cast method for your parts? Wondering how permanent mold castings can save you money? Here are 8 reasons worth considering!
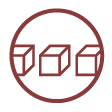
1. Higher Production Rates
Permanent mold means the mold doesn’t have to be remade each time- it’s permanent! As a result, higher production rates are possible. Additionally, permanent molds can produce tens of thousands of parts throughout their lifetime.

2. Lower Labor Costs
Higher production rates mean productivity is increased. Therefore, increase productivity results in a lower part price.
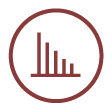
3. Weight Reduction
The higher strength properties produced by the permanent mold process allow for castings with thinner walls. The resultant weight savings ultimately means cost savings- both in material costs and shipping costs.
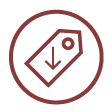
4. Lower Machining Costs
Closer dimensional tolerances made possible by permanent mold casting as well as the option of casting inserts such as threaded steel inserts, nuts and bushings into the casting minimize required machining and post-ops.
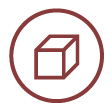
5. Smoother Surface Finish
Smoother “as-cast” surface finishes, typically 125-300 RMS reduce polishing costs.
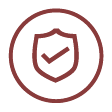
6. Soundness
Of the three basic types of castings, die, sand and permanent mold- permanent mold gives the soundest casting overall. Additionally, check out the Casting Method Comparison to see which process is the most suitable for your product.
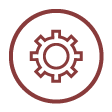
7. Strength
The chilling effect of the metal mold produces fine grain structures which significantly enhance physical properties. Elongation is 50%-100% greater and other mechanical properties are from 20%-25% greater than sand castings of the same alloy. In addition, heat treatment further enhances those properties.
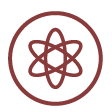
8. Low Porosity
Permanent mold castings are less susceptible to gas entrapment than that of sand castings or die castings.
Request Information
Ready to see how much money permanent mold can save you?
Talk with one of our casting specialists today!
"*" indicates required fields