Permanent Mold Castings: A Pathway to Quality
By Darell Gilbert, Plant Manager, LA Aluminum Casting Co.
As reprinted Technology Tips from Metlfax – original reprint here.
The casting approach enables metal to be put where it is required by part function in contrast to other processes that produce shapes more rigidly constrained by the limitations of the production process.
In selecting a method of producing parts, many factors must be taken into account. A major reason for selection of castings is their close approximation to the shape desired by the designer. Also, the wide range of casting methods and castable metals has earned the process a key role in parts manufacture.
An outstanding performer in the medium production range is the permanent mold process. For quantities from a few hundred, up to hundreds of thousands, permanent mold aluminum castings often provide the maximum combination of economy and high quality. A look at the nature of the process and the requirements of mechanical equipment reveals the specific reasons that favor the selection of permanent mold aluminum castings.
Cost and quality
Gray iron castings are usually thought of as being the cheapest castings available. However, when cost of providing a function is considered, aluminum castings often prove to be more economical or as economical as gray iron castings. When considering the economics of competitive aluminum casting process, permanent mold casting occupies a unique place. Usually, the cost of a permanent mold casting is less than a sand casting (often substantially less), and usually higher production rates can be obtained. However, the cost of tooling for sand casting is less than that for permanent mold.

When compared to die casting, permanent mold tooling is dramatically lower than die cast tooling, but the piece prices are somewhat higher. It is the combination of these two cost factors, piece price and tooling costs, that enables permanent mold castings to be extremely competitive over a wide range of medium quantity orders.
Each of the casting processes has a particular combination of properties in addition to the cost factors just mentioned. When quality (strength and soundness), is the key consideration, permanent mold aluminum casting stands out as clearly superior to either sand or die casting. This is so because strength in castings (alloy and heat treating being held constant), depends on two considerations:
- Fineness of metallurgical grain structure.
- Absence of voids caused by shrinkage or presence of gas or air.
A fine grain structure is obtained when castings are cooled rapidly from a molten to a solid state. The iron or steel of permanent molds draws away heat rapidly from the aluminum which creates a fine grain structure in the aluminum casting. In contrast, aluminum cast in sand requires much more time to solidify, which allows a coarser grain structure to form. Hence, sand castings are not as strong as those of the same alloy cast in permanent molds.
For example, 356 T6 aluminum alloy sand cast will typically provide an ultimate tensile strength of 33,000 psi. The same alloy cast in permanent mold will have an ultimate tensile strength of 38,000 psi. Yield strength in sand will be 24,000 psi compared to 27,000 psi in permanent mold. Elongation of the alloy sand cast is 3.5%, while the permanent mold value is 5%. Compressive strength values are 25,000 psi and 27,000 psi, while sheer strengths are 26,000 psi and 30,000 psi.
Although metal dies are used in the production of die castings, comparable strengths cannot be achieved by the process. The metal near the die cast surface does exhibit a fine grain structure. However, when molten metal is injected into the die cavity under pressure, air often becomes entrapped in the metal. Also, after the metal is injected into the die, additional metal cannot flow into the cavity as cooling and shrinkage take place.
As a result, die cast parts have good strength and soundness near the surface, but the more central portions of the castings often contain voids caused either by entrapped air or gas, or by metal shrinkage. This lowers the mechanical properties of the castings and may also cause blistering during heat treatment.
Reservoirs of molten metal (called risers), are used in both sand and permanent mold casting to supply additional metal as cooling and metal contraction take place. This enables both sand and permanent mold castings to be made without shrinkage voids of the type often present in die castings.
Entrapment of air is not a problem in pouring of either sand or permanent mold castings. However, sand molds can generate gasses that can be entrapped in the metal.
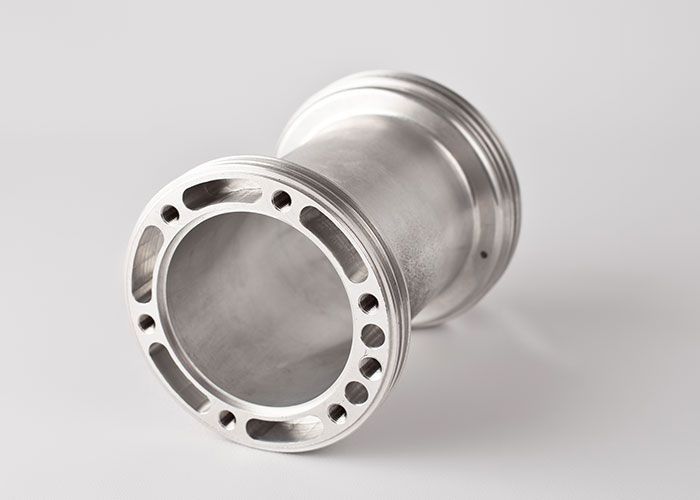
Textile rolling spool castings are pressure tested before shipment.
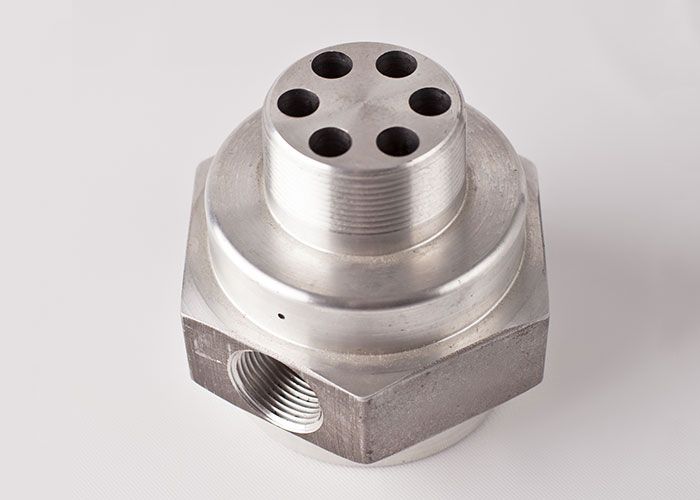
Diesel engine preheater castings cast using reverse tilt pour method.
Additional comparisons
There are several major reasons why aluminum castings have replaced iron castings (and are likely to continue to do so).
Weight savings is often the first reason designers look to aluminum. Density of aluminum is about 39% that of gray iron, or conversely, a shape weighting 10lbs. in aluminum will weight about 26lbs. in gray iron. In practice, however, substitution of one material for another will not necessarily follow the 1.00 to 2.58 density ratio.
Sometimes the aluminum casting must have ribs added, sections made thicker, or inserts used in order for the desired functions to be accomplished. Such changes will reduce the weight savings below that anticipated by following the weight ratio.
On the other hand, many casting designs are dictated by the needs of the foundry, often causing heavier designs in iron than are needed to meet the needs of the application. In these cases, the better castability of aluminum enables thinner sections (well ribbed for rigidity), to be used. Weight savings can be increased to as much as 1 to 5 or 1 to 6 compared to iron.
While the value of less weight in the finished part is usually well understood, as in the trucking industry where additional payloads are made possible with weight savings on truck parts, sometimes savings are neglected. For example, freight costs to the point of manufacture may be documented, but freight costs of the completed product to the end user may receive scant consideration. Or the savings made when replacement parts are shipped by air may be well understood, but the manufacturing savings made possible by lightweight aluminum are ignored.
As an example, an aluminum casting weighing 30lbs. can be moved by hand through a machine line, while a 75lb. iron casting would call for the use of hoists. Similarly, the light weight of aluminum often makes it possible to do equipment repairs in the field, which would not be possible if gray iron castings were involved.
Machining costs of aluminum castings are often the major factor in making aluminum competitive with gray iron. Usually, aluminum sand and permanent mold castings cost more than equivalent iron castings before machining. However, machining costs of aluminum are often substantially less (ranging in 40% less), than the costs of machining equivalent gray iron shapes. As a result, casting plus machining costs of aluminum are often comparable to, or less than, gray iron costs.
The better castability of aluminum castings makes possible closer tolerance control and better surface finish, and as a result, less machining stock (often 50% less), is required. In addition, aluminum alloys have better machinability ratings and can be machined at higher rates with equal tool life than can gray iron castings.
Depending on the type of cutting operation, metal removal rates of aluminum castings are two to seven times faster than those of Class 20 gray iron. Considerably less energy is required for machining aluminum than gray iron. Horsepower requirements for removing an equal volume of aluminum are from 1/3 to 1/10 that of gray iron.
The advantages of aluminum are often best demonstrated by examining specific applications. For example, the good thermal conductivity of aluminum castings makes them particularly suited for use as transmission cases or for cooling system parts in truck engines.
The good ductility of aluminum leads to its use for hand tools and similar applications. Also, the attractive appearance and corrosion resistance of aluminum castings have led to their use as control levers and equipment covers.
Strength, corrosion resistance, and thermal conductivity are the reasons for the use of aluminum castings for radiator tanks and side-frame supports.
A major reason for the use of aluminum castings in tractors and construction equipment is their contribution to the lowering of the center of gravity of such equipment. Other parts that are made of aluminum include pistons, flywheels housings, timing gear housings, oil pans, intake manifolds, torque converter impellers, and turbo-charger compressor housings and wheels.
Review our Casting Method Comparison and other FAQ.
Request Information
Talk with one of our casting specialists for more information.
"*" indicates required fields